Backflow Repair
A backflow assembly needs to be tested annually and if the test fails, the backflow device repair is called for. Repairing of a good backflow device means taking it apart and fixing it back, hence it is pertinent that the plumber performing the repair is certified. The backflow repairing professional should be well adept with the different manufacturers of the backflow prevention devices, particular assembly & models manufactured over the years. Depending on the model, some backflow prevention assemblies may rarely need repair while some are repaired on a regular basis.
Steps of repairing a Backflow Prevention Device
The repair technician would first shut down the water supply. The consumer is informed in advance so that they can make arrangements. Sometimes these repairs are planned in odd hours so that the regular business activity of the consumer is not affected.
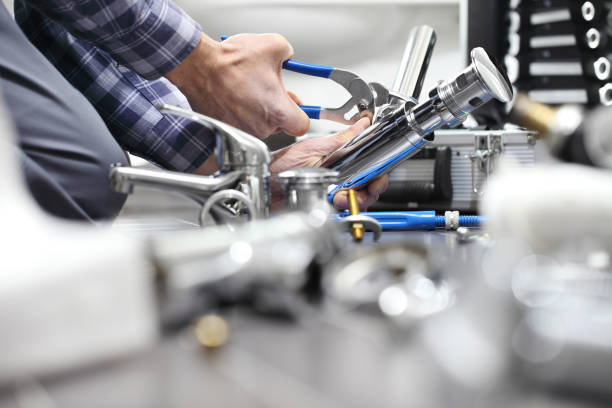
Our technicians are well certified and trained. They will have a full working knowledge of the assembling and disassembling of the backflow preventer. This is a must to ensure that no spring tension is released prematurely, or any part which does not need to be removed is removed, and to ensure that the disassembly is done in the right order.
The backflow repair plumber will release all the pressure from the assembly and will then remove the components from the assembly. The working of each component will then be inspected individually for the reason of the failure of the backflow device.
The component would be then taken apart to inspect each part for wear and tear, corrosion, scaling etc. The parts are cleaned properly with a soft material to ensure there are no scratches. It is imperative for the repair professional to understand whether the part can be cleaned and put back to use or would need a replacement. It is a good idea to replace old rubber parts with the new ones for longevity of the entire components
After a thorough inspection, cleaning and changing of parts (if needed be) the component is assembled back again, component seats are evaluated, the incoming water line is flushed. This part could be tricky especially if the backflow prevention assembly is installed in a place where it is not feasible to have water splashing around.
A good food grade lubricant is also an essential part of the repairing process, which ensures that the components are assembled back without any damages and also to ensure there is no contamination to the water supply. But using too much of it may also attract dirt and debris and failing of the components. Hence it is critical to understand how much and where it has to be used.
Once the technician is certain that everything is in place, the next step is to pressurize the assembly and remove the accumulated air from inside the body. The technician must know about all the air bleeds and air screws designed in the body to release the air. Hence is it very important that the technician is well trained and knows the device assembly in and out
After all is done the backflow prevention assembly is tested again to confirm that it meets the originally factory specifications. The final test report is entered in the test results with a detailed brief of which parts have been replaced.